A LiDAR with high resolution for the near environment up to 25 m should increase the safety of autonomous and semi-autonomous vehicles. The result is a minimally complex system.
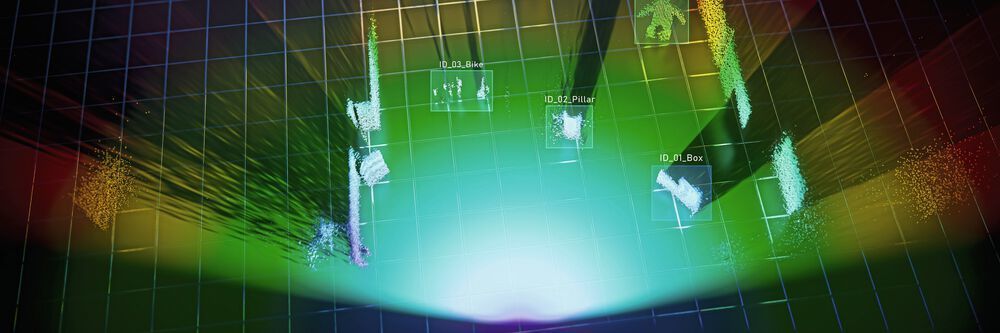
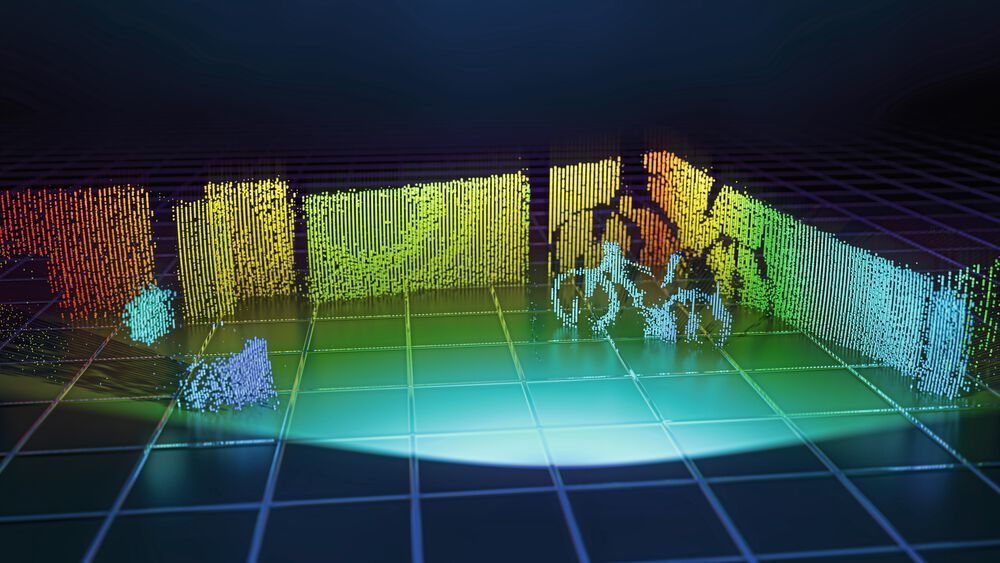
Automotive car manufacturers want to use LiDAR systems to advance semi-autonomous and autonomous driving. The basis is 3D object recognition using LiDAR technology.
A large number of such sensors are currently required for the pilot and test phase, such as robot cabs, which unfortunately are not yet suitable for the mass market in terms of both price and performance. Within the framework of the Research Fab Microelectronics Germany (FMD), a proof-of-concept project for a high-resolution wide-angle LiDAR system started. The MEMS start-up OQmented was responsible for the project planning and the integration of the components contributed by the participating institutes.
The Ferdinand-Braun-Institut provided a pulsed laser source including a control electronics, the Fraunhofer Institute for Microelectronic Circuits and Systems IMS contributed a SPAD array with pre-processing electronics and the Fraunhofer Institute for Silicon Technology ISIT produced the MEMS scanners, which are exclusively commercialized and further developed by OQmented. The project was implemented within the framework of the FMD-Space to support start-ups and is coordinated by Stephan Guttowski and Christoph Galle.
Focus on short-range LiDAR
The project aimed to demonstrate the performance of the world's first 180°MEMS scanner. Start-ups and Tier 1 companies have focused on detecting long distances in recent years. The ranges exceeded 250 m and more. However, the important short to medium range of a vehicle was neglected. According to OQmented, the short and medium distances are particularly important for road safety. This is where currently camera and radar systems are being used, but these have various disadvantages. These include insufficient resolution and a lack of night vision. For example, right-turn situations with a blind spot to other road users and complex intersection situations in city centers are just a few cases in which the close range of a vehicle in a high-resolution image are of particular interest.
A minimally complex overall system
At its core, a LiDAR system consists of a laser, a scanner, and a receiving optics, which communicates with each other via electronic components. Most LiDAR systems consist of a large number of lasers and optoelectronic components, which are complex to manufacture and cost-intensive. In addition, such a system must be appropriately qualified for the use in series production of a vehicle.
OQmented’s approach pursues a radical reduction of overall costs and system complexity. The chosen approach is limited to one component at a time, which were introduced as standard components. Thus, no pre-development is necessary to coordinate the interaction.
The following components were combined for the first time:
- 905 nm wavelength stabilized laser with less than 30 W peak optical power,
- 1D resonant MEMS scanner with a Field of View of 180° and a hermetic vacuum encapsulation and
- 192 x 2 CMOS SPAD detector with a TDC resolution of 312.5 ps.
The project lasted twelve months, from the concept, development and setup phases to the final demonstration. In the process, the team members were able to expand and improve the LiDAR system through easy-to-implement adaptations.
With 140° of the horizontal field of view (FoV), it can be increased via improved imaging optics. Vertically, the FoV was 15° and it can also be improved by an optimized laser source. According to the above components, the horizontal resolution of 0.5°, vertical 0.25°, can be significantly increased and a target of 0.1° can be achieved. The range is 25 m but can be increased by improved signal-to-noise ratio.
Further miniaturize LiDAR system
The results of the proof-of-concept provide a solid base to be transferred for industrial use. In addition, the LiDAR system can be further developed. The starting points for a go-to-market strategy and thus a successful project outcome are to further miniaturize the overall system and increase the frame rate.
The goal is to reduce the related standard components to a size relevant to system integration and performance requirements. With improved component tuning, especially at the electronics level, a frame rate that meets automotive requirements can be achieved. The final step towards market introduction is the qualification for system integration in an automobile or truck, for example to reliably detect blind spots when turning right.
The project on which this publication is based was partly funded by the German Federal Ministry of Education and Research under grant numbers 16FMD01K, 16FMD02 and 16FMD03.